
Riser Design Metal Casting Production Process 1 YouTube
A riser (or feed head) is an opening through the cope. Its main purpose is to feed the molten metal to the casting as it solidifies i.e., to compensate for the shrinkage. The risers also serve as a large vent for generated steam and gases and afford a place for collecting loose sand or slag.

Cloud Comfort Multi Function Riser Recliner Murrays.ie
Contents show Riser Riser is a source of extra metal which flows from riser to mold cavity to compensate for shrinkage which takes place in the casting when it starts solidifying. Without a riser heavier parts of the casting will have shrinkage defects, either on the surface or internally.

Casting modulus
A riser in the casting process is a passage in the casting mold which prevents casting shrinkage defects and is designed into the casting mold. Once the liquid metal has solidified, the riser is removed from the mold. A riser reduces the number of defects in the casting materials, hence improves the number of defect-free products of the process.
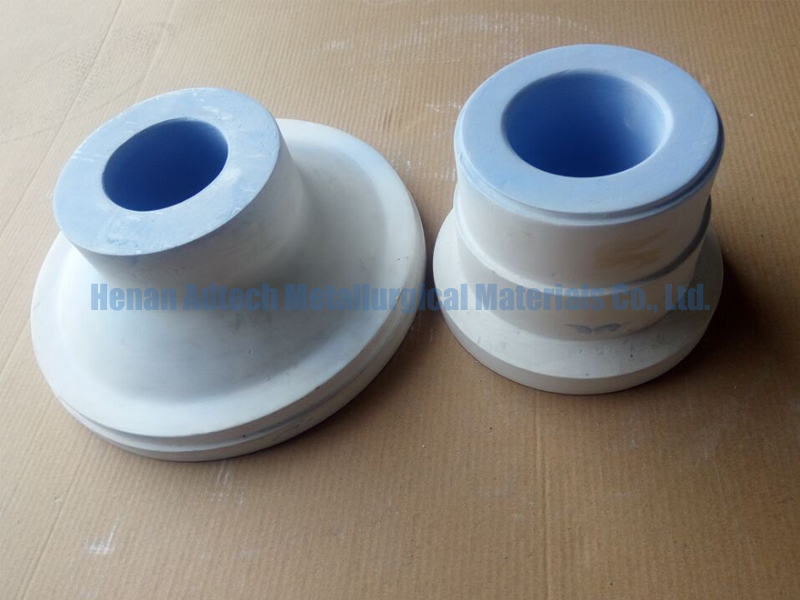
Alumina Ceramic Parts Riser in casting Aluminium Adtech China
A riser, also known as a feeder, [1] is a reservoir built into a metal casting mold to prevent cavities due to shrinkage. Most metals are less dense as a liquid than as a solid so castings shrink upon cooling, which can leave a void at the last point to solidify.

PPT FUNDAMENTALS OF METAL CASTING PowerPoint Presentation, free download ID480465
The primary function of riser as attached with the mould is to feed molten metal to accommodate shrinkage occurring during solidification of the casting.
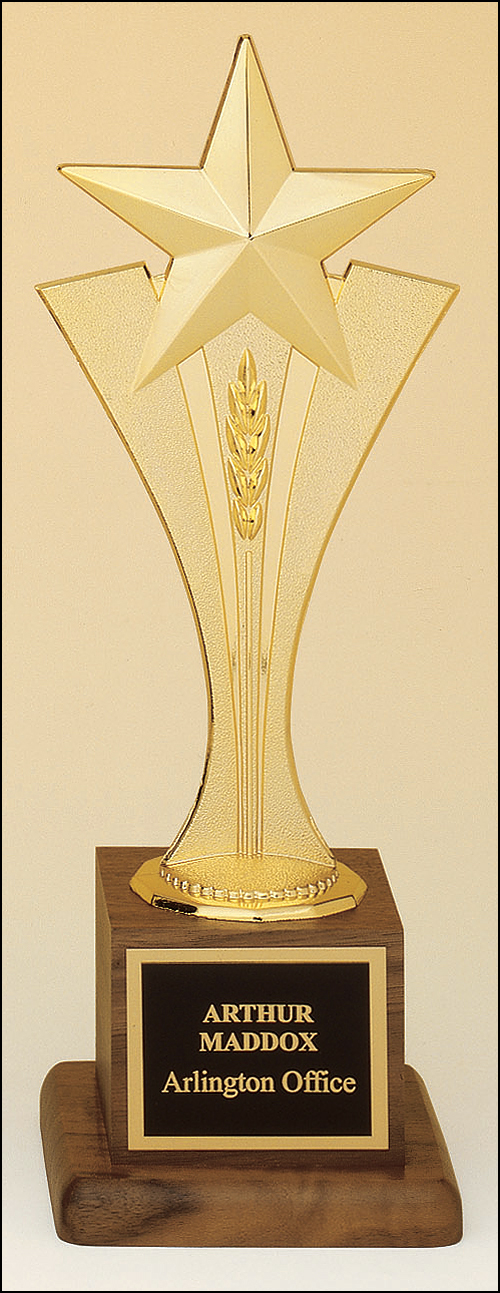
Metal goldtone star riser casting on a solid American walnut base. Twin City Awards & Trophies
Functions of riser: Riser ensure the complete filling of the cavity so that the sound casting can be produced. Clearly riser functions can be divided into four categories. Used to compensate shrinkage (Liquid and solidification). Ensure complete filling of the cavity. Make the dense/compact casting.
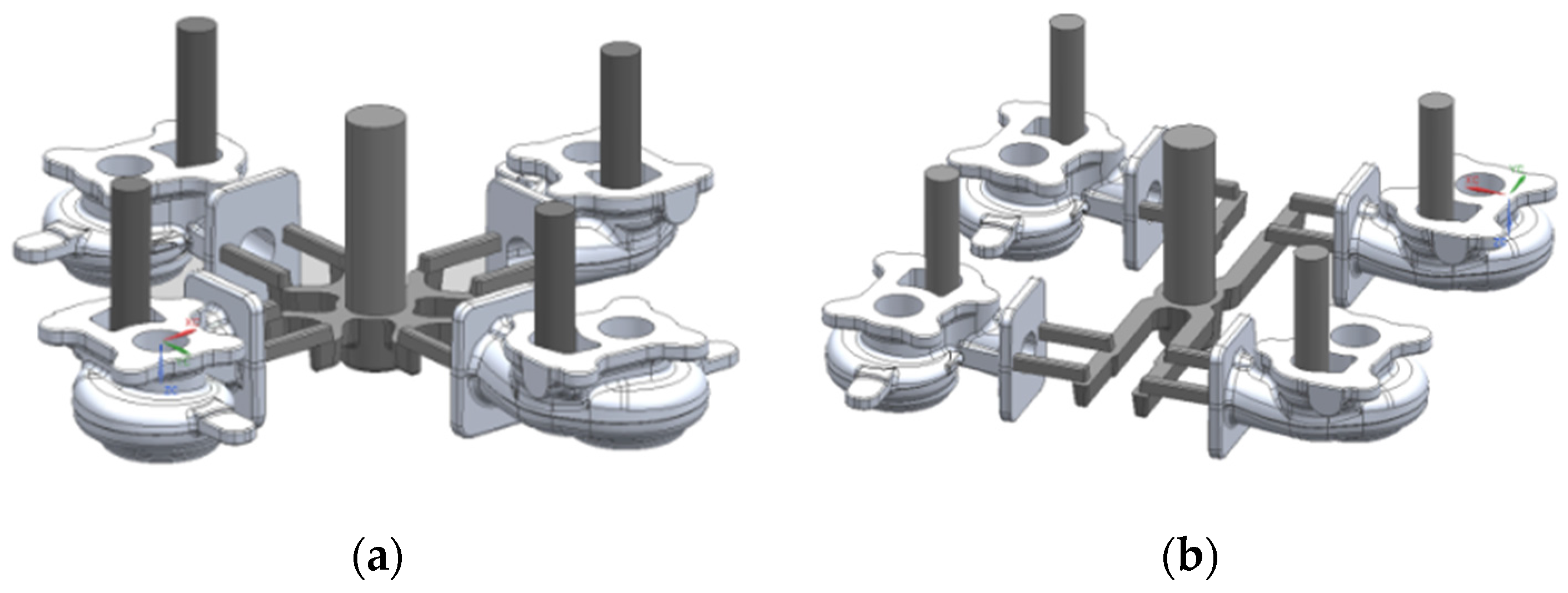
Metals Free FullText Heating System for Riser Size Minimizing in Sand Casting Process and
Risering Iron Castings This module identifies the uniqueness of feeding graphitic cast iron alloys. The three ways that risers should be designed for cast iron are explained along with the factors that affect volume change. By the end of this module, you will be able to list unique riser considerations for iron castings. (0.1 CEU)
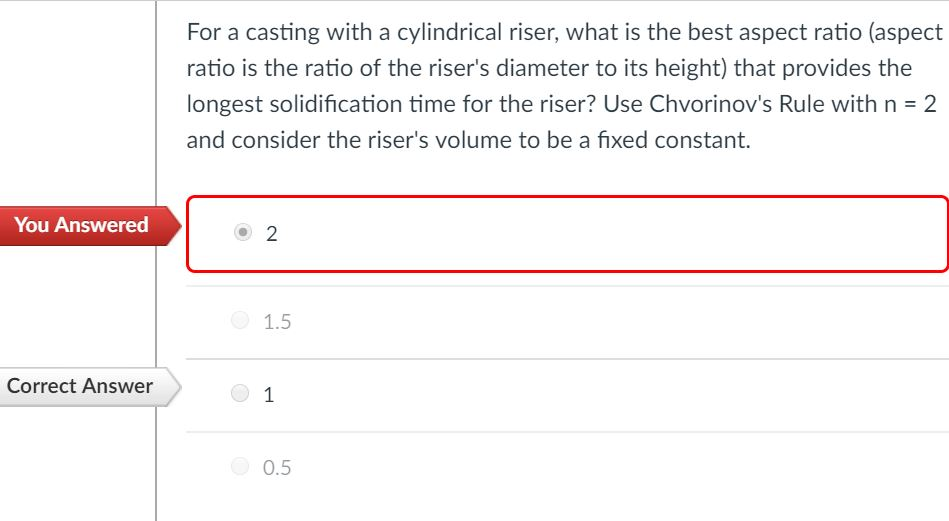
Solved For a casting with a cylindrical riser, what is the
Riser Design (Casting) Definition: Riser is defined as a reservoir for supplying molten metal to the casting cavity to compensate (additional molten metal) the liquid shrinkages taking place due to solidification. Shape of riser: It's shape is almost cylindrical since it takes more time to solidify than sphere and cube shape.
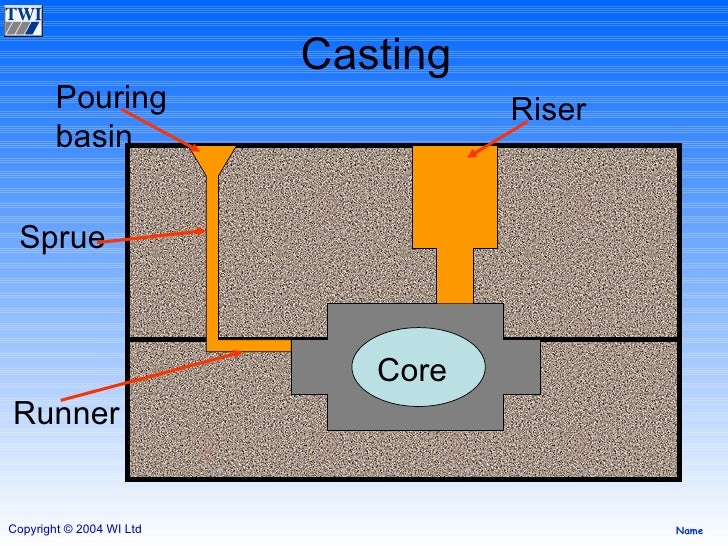
Ut P5 (Product Tech.)
open access โข This paper deals with the interconnection between the manufacturing industries (casting) and the concept of optimization. โข It aims to bring out the use of various software that helps the production industry design and analyse the overall casting process.
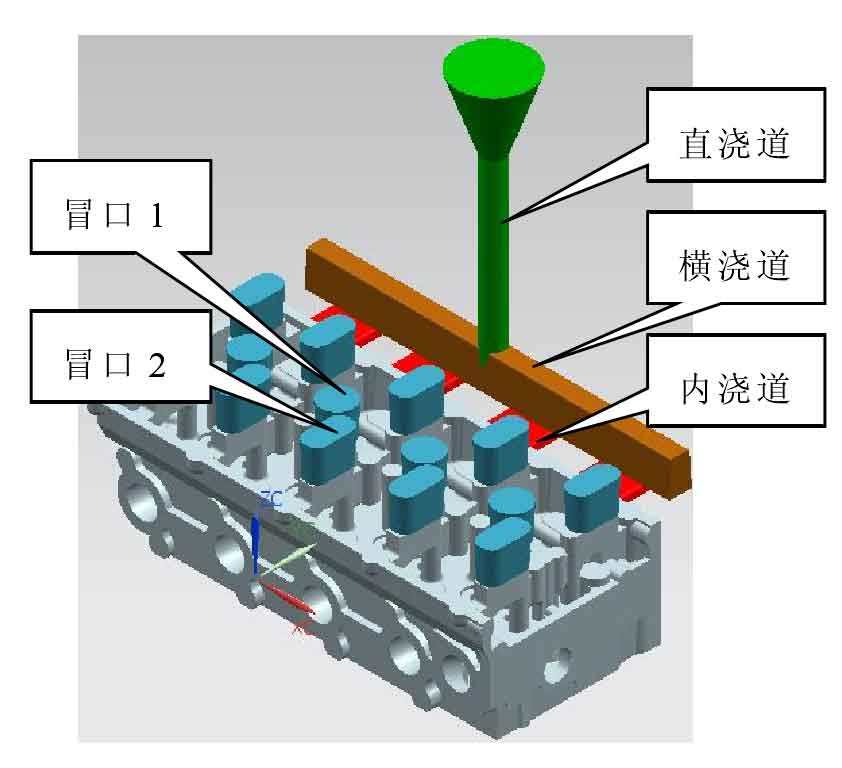
Design of riser in sand casting ZHY Casting
A riser is a static reserve volume of metal available to flow into the casting to compensate for shrinkage as the liquid freezes. Risers are relatively large because they should not freeze until after the casting has frozen. Risers may be "hot topped", exothermic material is put on to provide extra heat to keep the riser liquid as long as possible.

Metal casting riser design calculation Riser design example problems YouTube
#modimechanicalengineeringtutorials, #mechanicalmagicmechanicallearningtutorials,Welcome to My YouTube Channel MODI MECHANICAL ENGINEERING TUTORIALS.This ch.
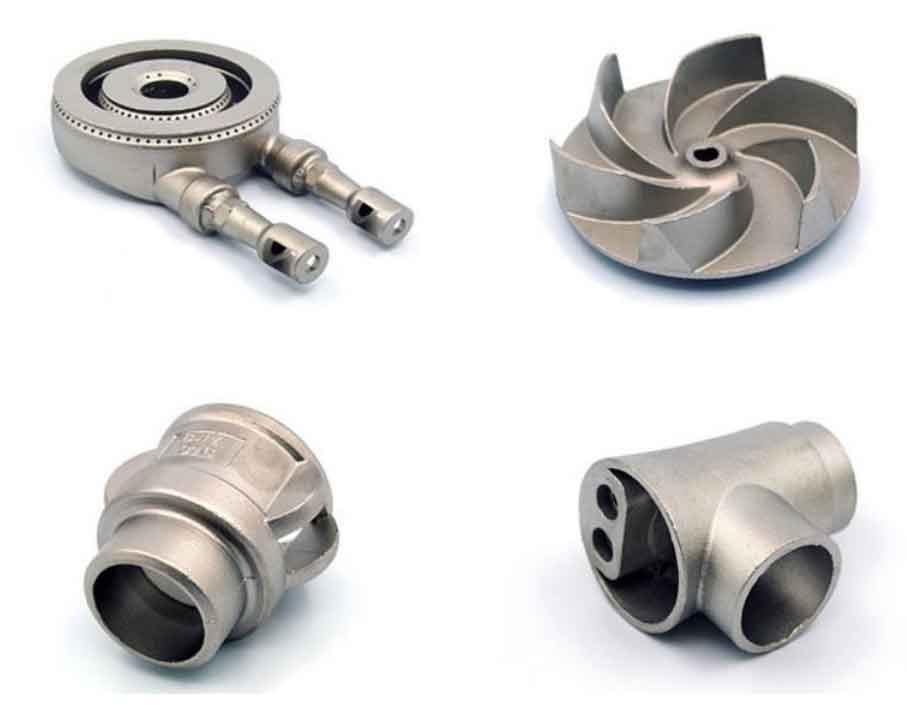
Riser design of casting process for cast steel joint ZHY Casting
BASIC THEORY OF RISER DESIGN Riser design for shrinking alloys is based on a simple premise; as metal cools and solidifies, it shrinks, or contracts. Risers must be large enough to solidify after the casting, or casting section, being fed, and must have enough volume to provide enough 'feed metal' to offset casting shrinkage.

Different Metal Casting Processes used in the Manufacture of Parts
Different ways to calculate the geometry of the riser . Casting is an important industrial process for manufacturing near net-shaped products such as engine blocks, crankshafts, and turbine blades. Among various shape casting methods, sand casting is very common, and more than 80% of casting parts is produced by this method [5]..
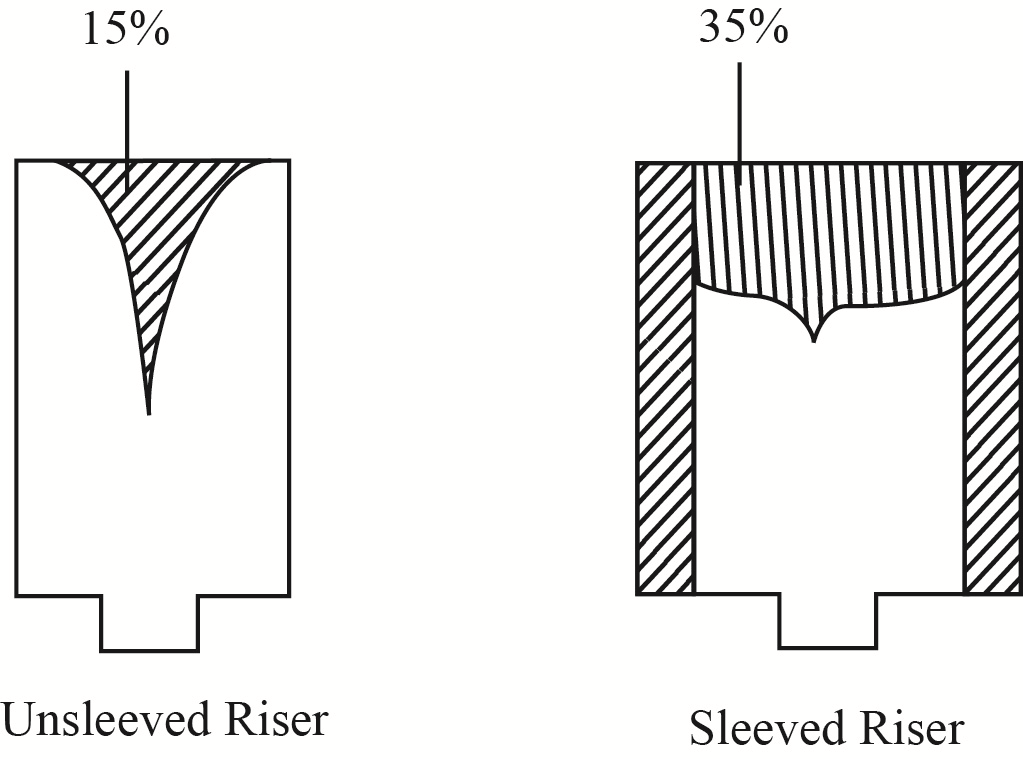
Solved Chapter 9 Problem 113P Solution The Science And Engineering Of Materials 7th Edition
About Press Copyright Contact us Creators Advertise Developers Terms Privacy Policy & Safety How YouTube works Test new features NFL Sunday Ticket Press Copyright.
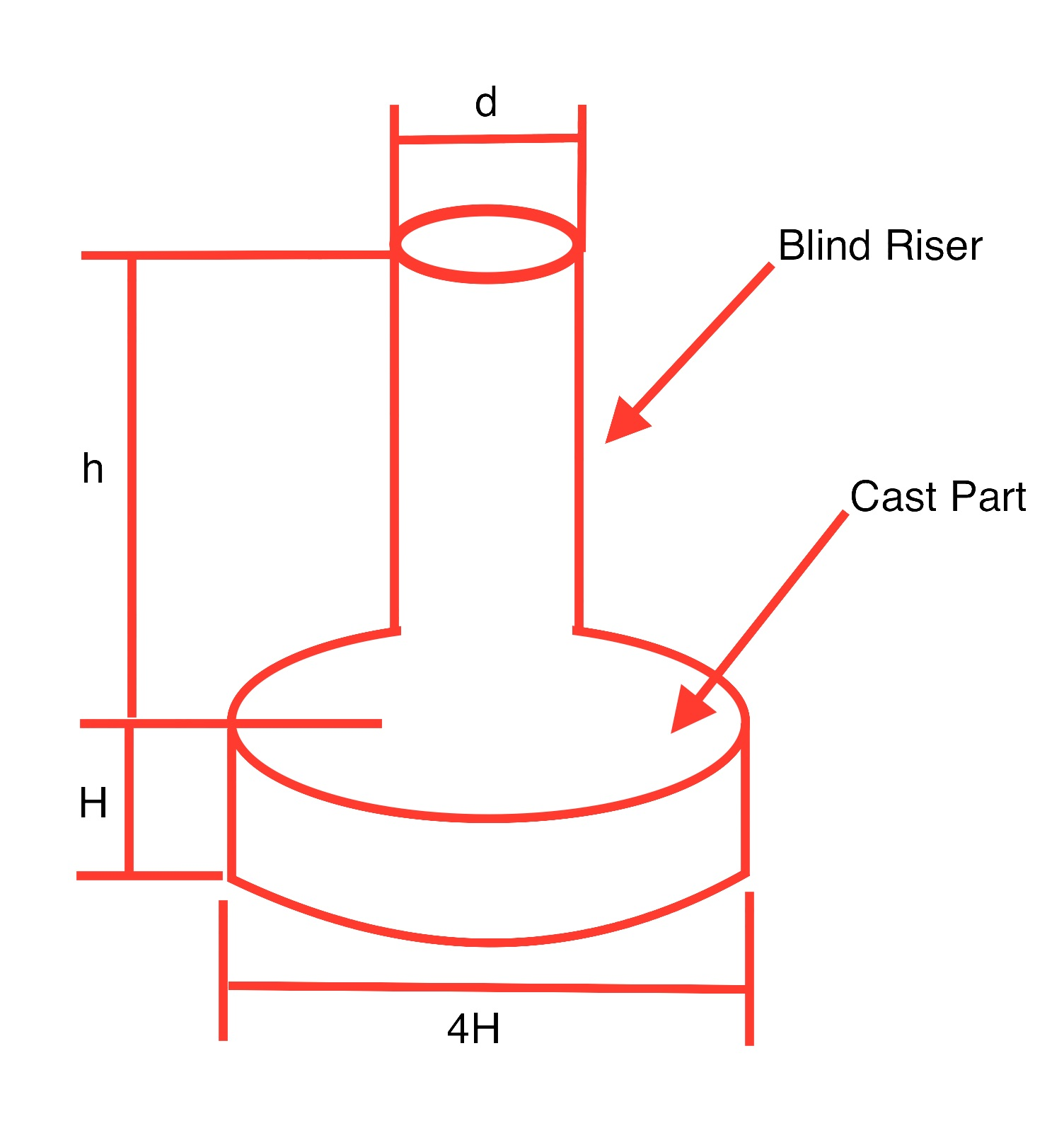
A cylindrical blind riser must be designed for a sand
Explanation : A riser, also known as a feeder, is a reservoir built into a metal casting mold to prevent cavities due to shrinkage. Most metals are less dense as a liquid than as a solid so castings shrink upon cooling, which can leave a void at the last point to solidify. What is difference between runner and riser?
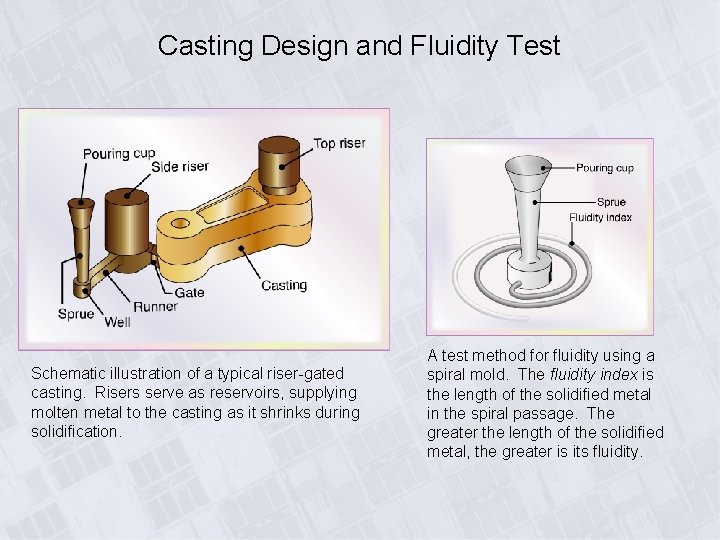
Chapter 10 Fundamentals of Metal Casting Copyright PrenticeHall
Risers and runners Published - 21st Jan 2016 In this blog, we take a look at the important role played by risers and runners in sand casting. Risers These are vertical channels that provide a continuous flow of molten metal to eliminate shrinkage as solidification occurs during the casting process.